QFD, the English acronym for Quality Function Deployment, is a system for designing a product or service based on customer requirements that involves all members of the manufacturing/supplier organization.
The system is explained by its very name:
Quality = meeting customer requirements
Function = what needs to be done
Deployment = Who, how, when will do
QFD was implemented for the first time in Japan, at the Kobe Shipyards belonging to the Mitsubishi company - between the years 1977 - 1984, reductions of 61% for product development cost and 33% for product development cycle time were achieved.
QFD was then widely adopted in the US and other countries in various fields of activity and is now integrated into the Design for Six Sigma (DFSS) framework.
QFD includes 4 stages, sometimes called "Houses of Quality"; these 4 stages deliver essential parameters and metrics for specific steps in product and process design/engineering.
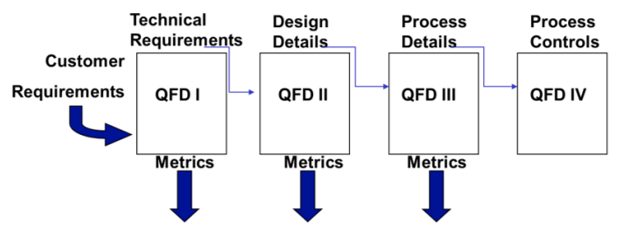
In order to successfully implement QFD, several basic conditions must be met:
- Clear understanding of customer needs
- A competent and available team
- A clearly defined and approved Project Charter
- Optimal conditions for working on the project, created by senior management
QFD is a powerful and reliable tool, fully aligned with DFSS and able to:
- Facilitate the development of new products and/or processes,
- Harness the power of creative group thinking,
- Disseminates customer requirements throughout the organization
- It provides product and process specifications that are more detailed and more closely aligned with the customer's needs